- Obtained manufacturing license
and GMP IT System
-
Competitiveness High-speed
automated
equipment -
Smart Quality Control GMP
optimized
IT solutions -
BACCHUS production
per year 320million
bottles
OTC drugs/medicinal drinks
-
Year of completion
- 2021
-
Site area
- 77,190m2
-
Building area
- 20,096m2
-
Production workers
- 84
-
Speed
- A/B Line – Each 1,200BPM
-
Key Products
- Bacchus D/F/Decafe
-
01
Weighing / Dissolving
- Weighing:
-
Use a scale to accurately weigh
and subdivide raw materials. - Dissolving:
-
Input the primary, secondary,
and tertiary raw materials to the water-soluble
and non-water-soluble dissolution tanks,
and transfer to the formulation tank
when completely dissolved.
-
02
Dispensing / Sanitizing
- Dispensing:
-
Transfer the dissolved primary, secondary,
and tertiary raw materials to the dispensing tank,
purge the 30,000 L and perform the final stirring to
complete the semi-finished product. - Sanitizing:
-
Sanitize the semi-finished product with
H.T.S.T 95℃ for at least 30 seconds.
-
03
Cleaning / Filling
- Cleaning:
-
Clean the inside and outside of the bottle with a bottle
cleaner and dry with air. - Filling:
- Fill the empty bottle with the set weight via the charger.
-
04
Capping
Using a rotating roller component that fits into the gap
between the threads of the bottle neck, apply pressure
in the direction of the threads to seal the product. -
05
Liquid foreign body
inspectionThis is a process of inspecting semi-finished bottles
for internal and external foreign bodies, contamination,
and undercapacity using a liquid foreign body inspector. -
06
Case Packaging
This is a process of arranging 10 bottles,
filling the 10-bottle case, molding, gluing, pressing
and printing with the production number
and expiration date, and discharging the bottles. -
07
Loading
This is a process of automatically loading, wrapping,
and discharging the box products fed along
a conveyor onto a pallet.
- Weighing:
- Use a scale to accurately weigh and subdivide raw materials.
- Dissolving:
- Input the primary, secondary, and tertiary raw materials to the water-soluble and non-water-soluble dissolution tanks, and transfer to the formulation tank when completely dissolved.
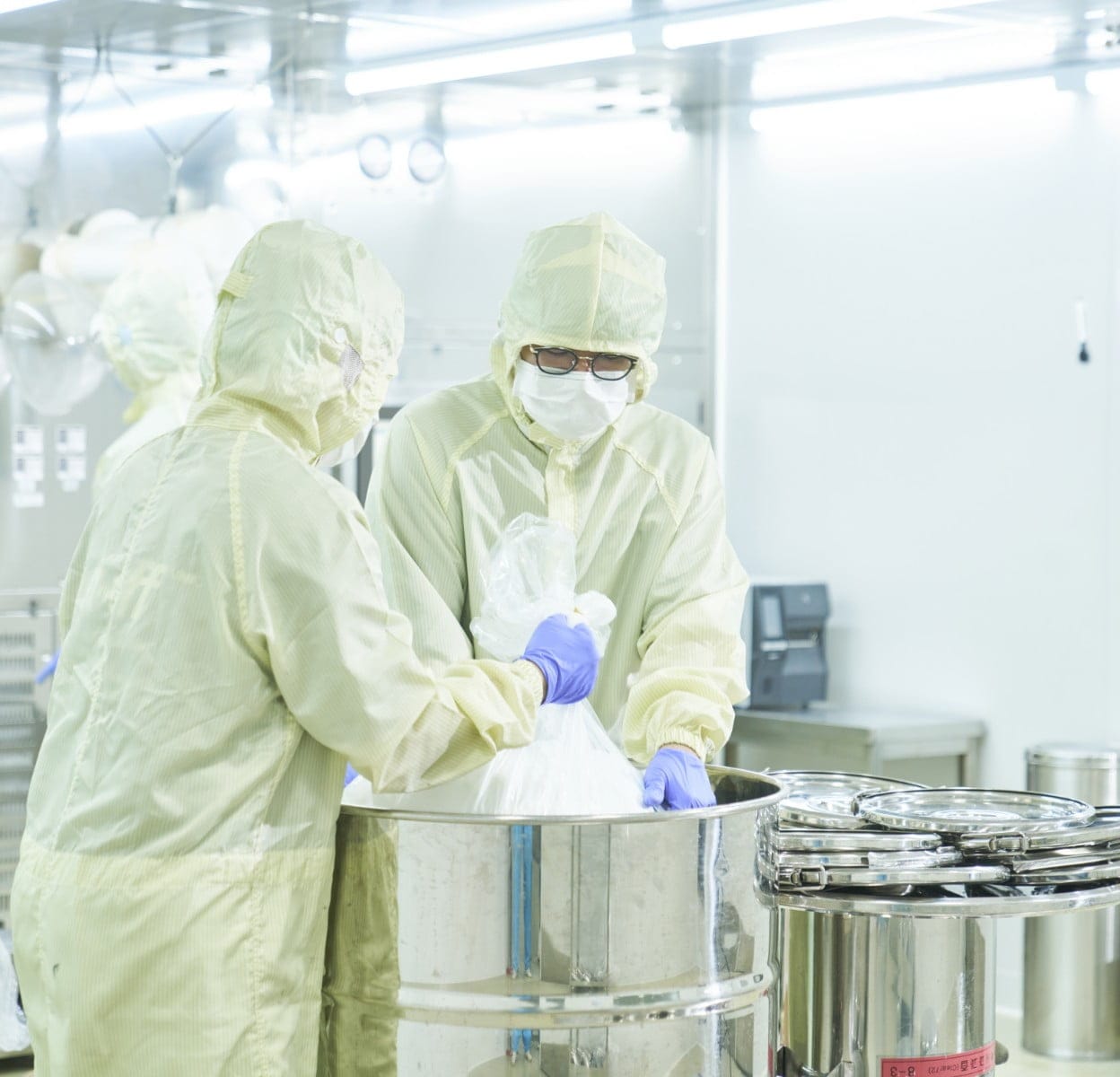
- Dispensing:
- Transfer the dissolved primary, secondary, and tertiary raw materials to the dispensing tank, purge the 30,000 L and perform the final stirring to complete the semi-finished product.
- Sanitizing:
- Sanitize the semi-finished product with H.T.S.T 95℃ for at least 30 seconds.

- Cleaning:
- Clean the inside and outside of the bottle with a bottle cleaner and dry with air.
- Filling:
- Fill the empty bottle with the set weight via the charger.
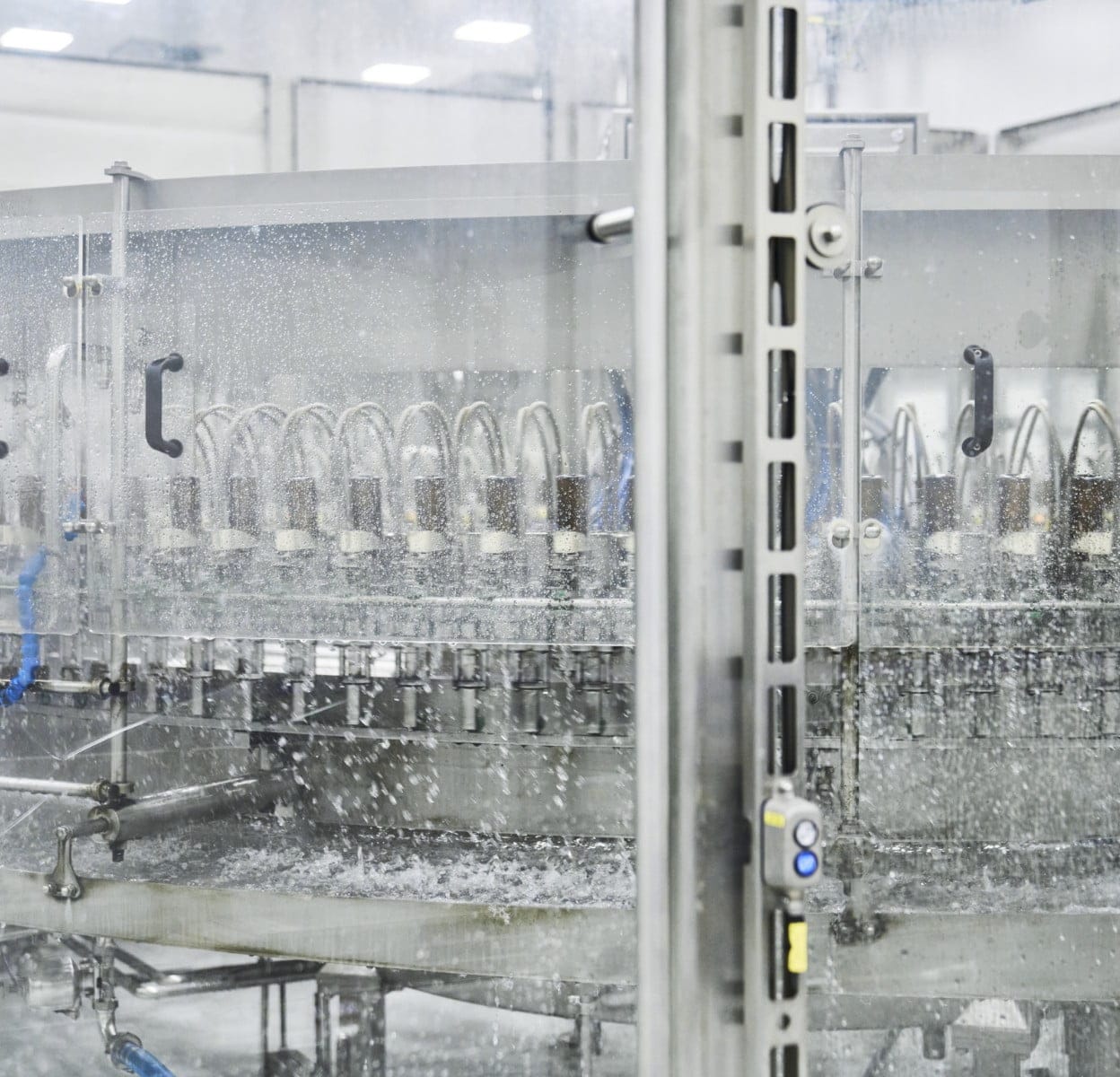
Using a rotating roller component that fits into the gap between the threads of the bottle neck, apply pressure in the direction of the threads to seal the product.
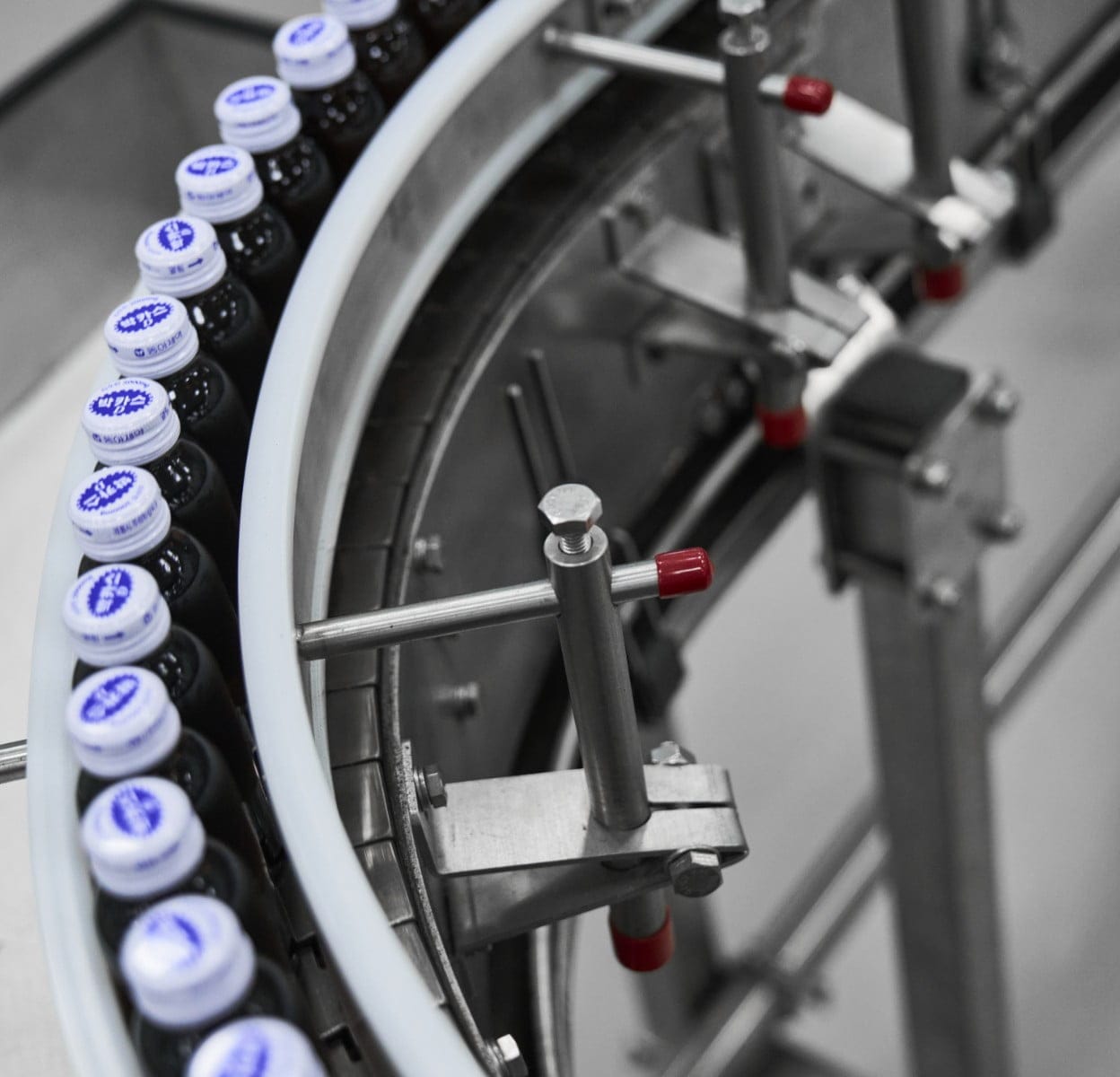
This is a process of inspecting semi-finished bottles for internal and external foreign bodies, contamination, and undercapacity using a liquid foreign body inspector.
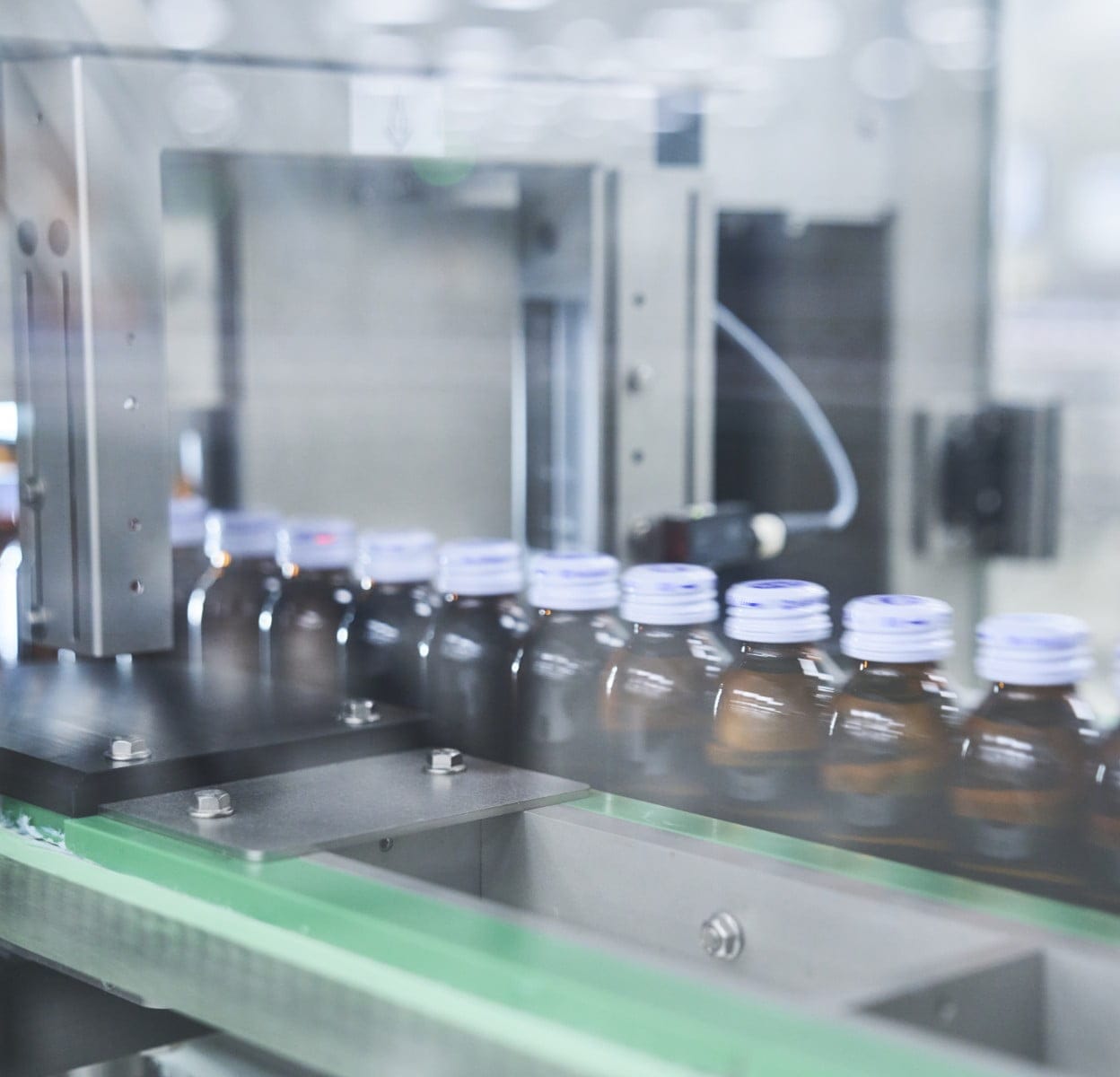
This is a process of arranging 10 bottles, filling the 10-bottle case, molding, gluing, pressing and printing with the production number and expiration date, and discharging the bottles.
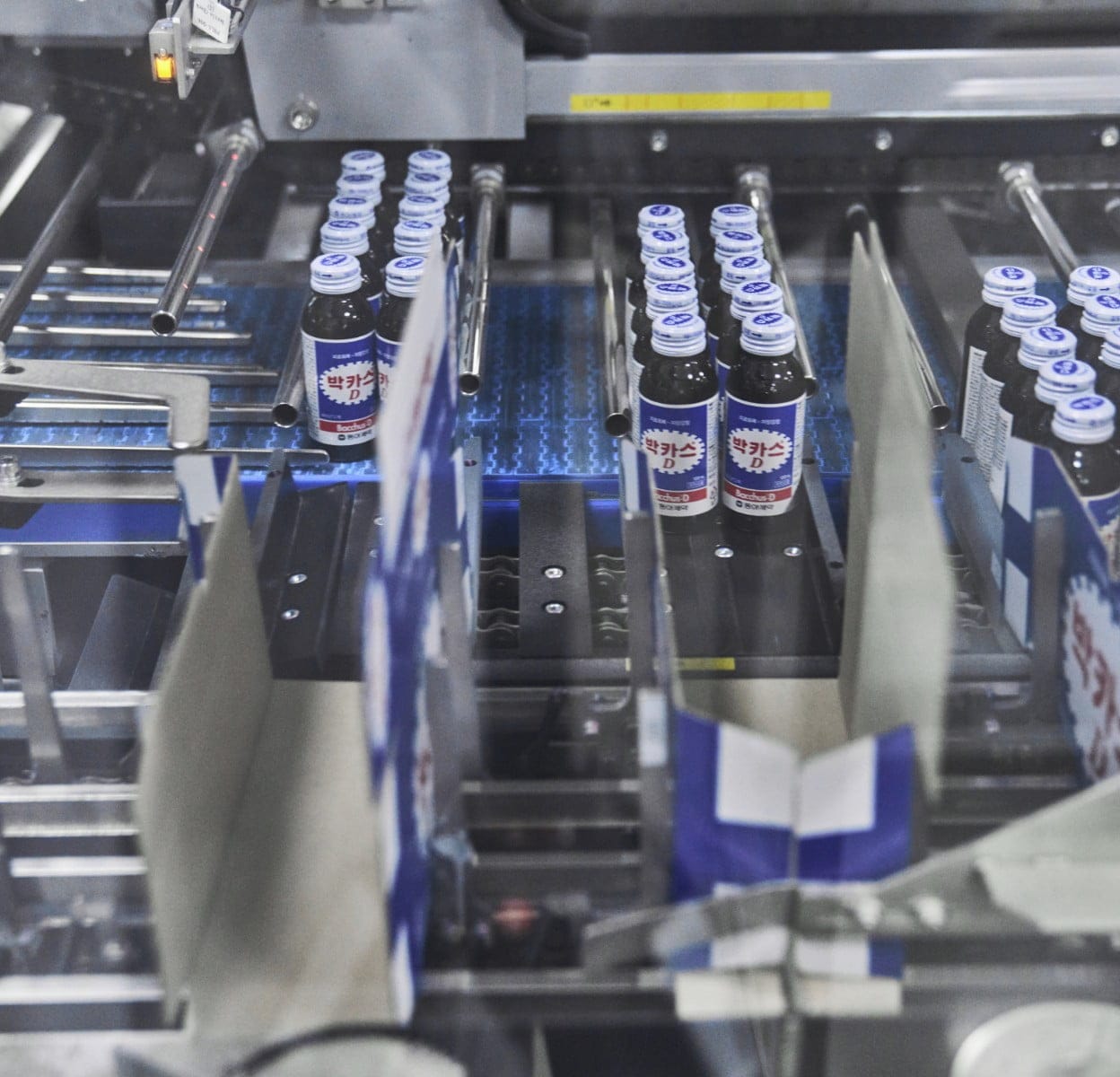
This is a process of automatically loading, wrapping, and discharging the box products fed along a conveyor onto a pallet.
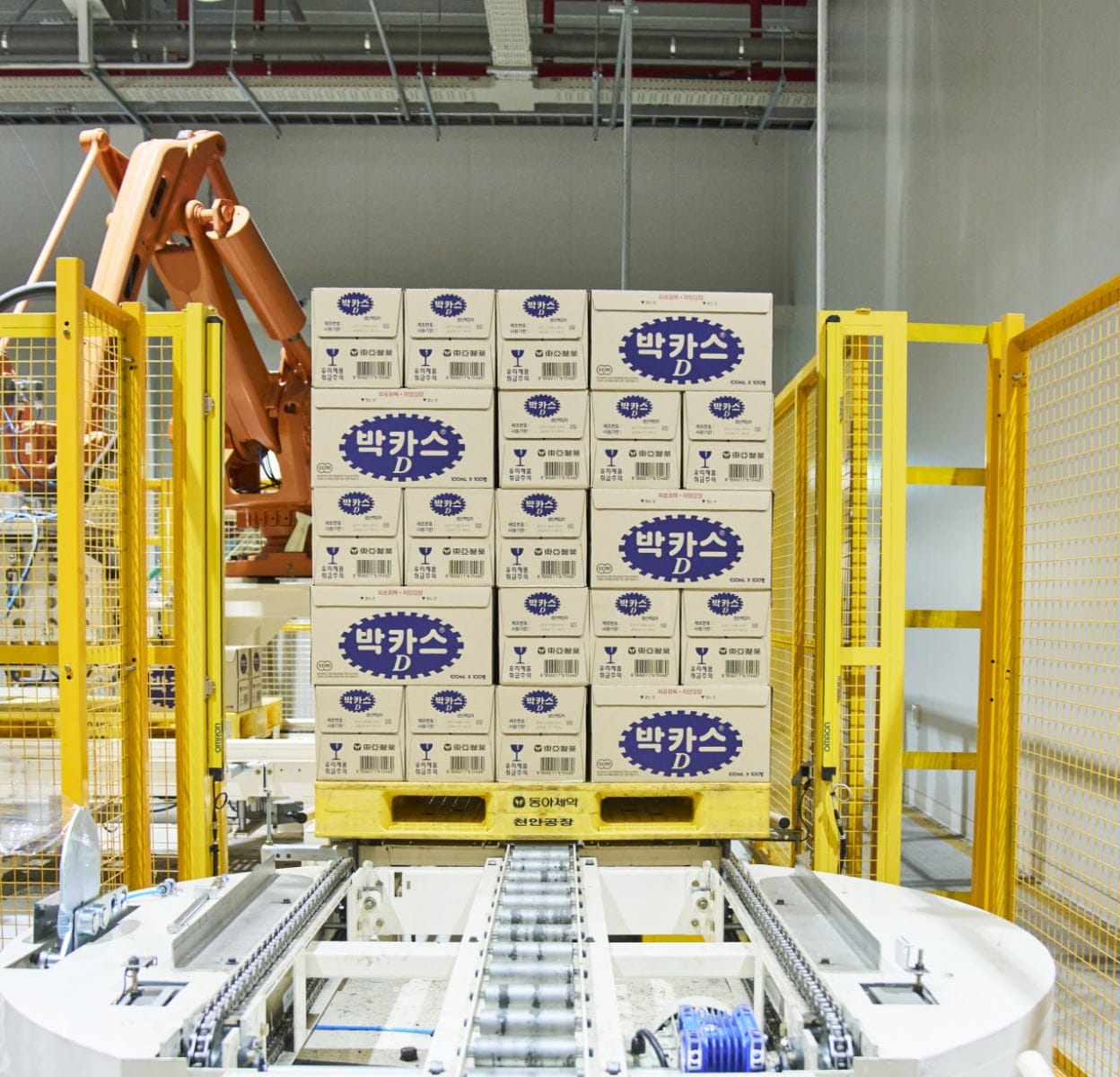
Watch the video to see the latest automation equipment and GMP IT System at the plant.
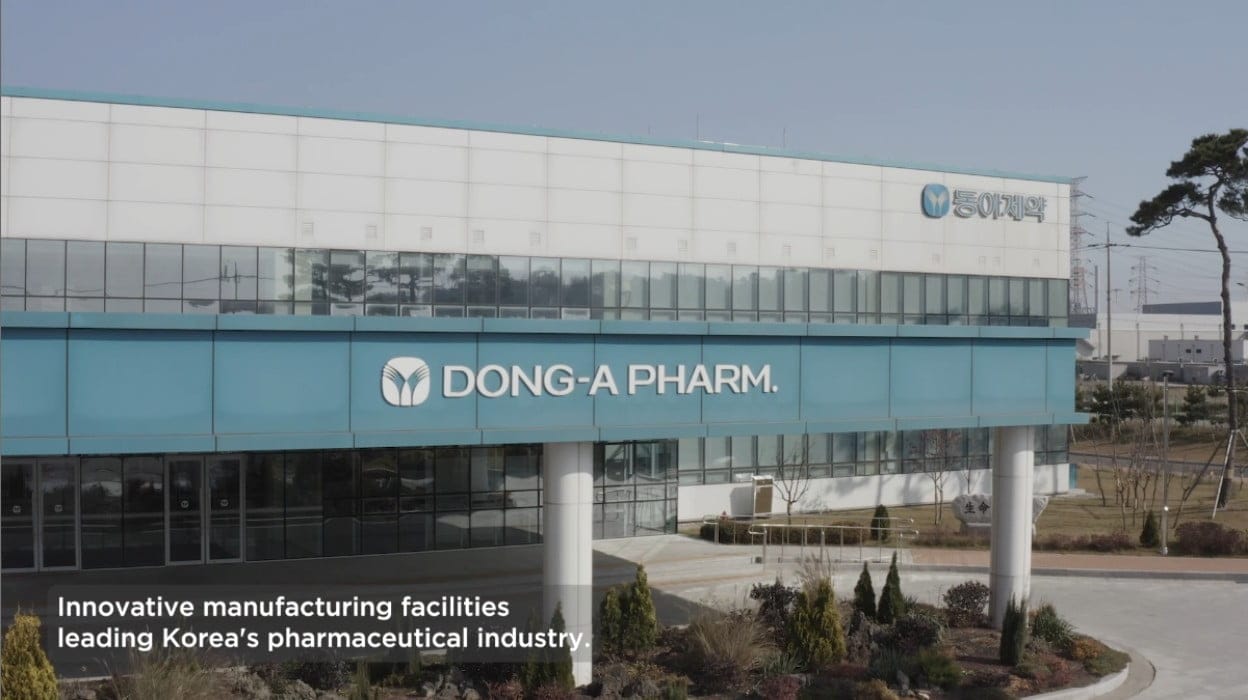